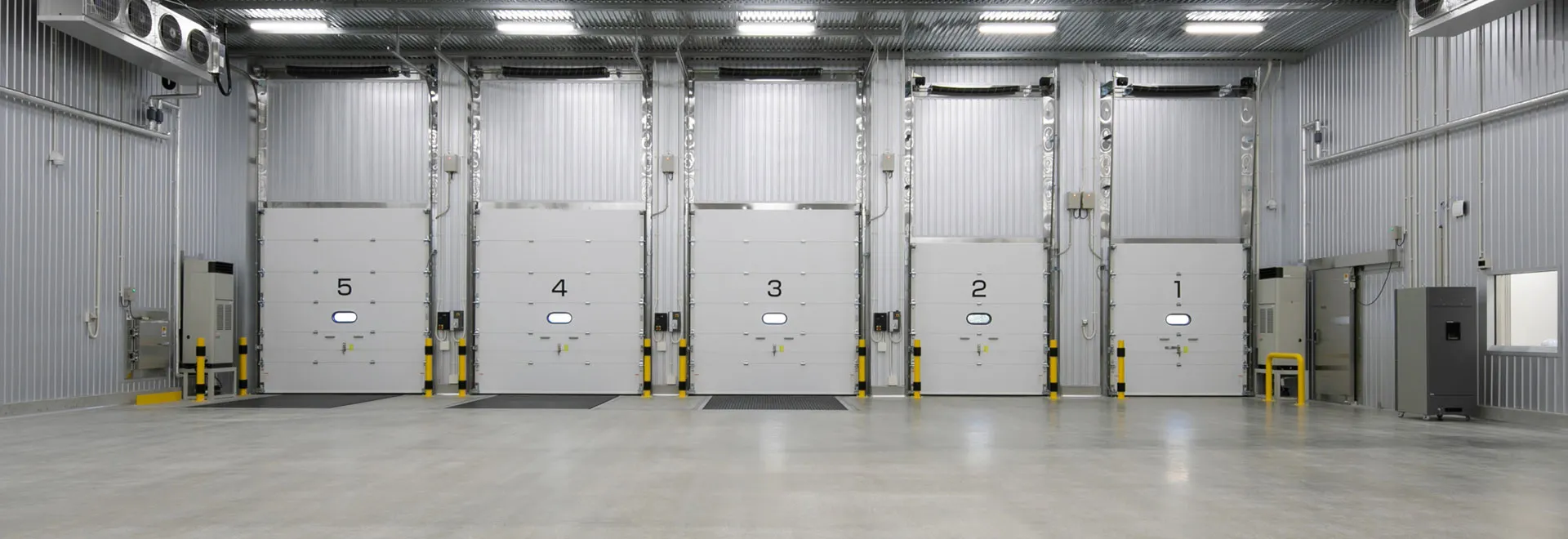
熱意が生んだサプライチェーン改革 途切れることのない食品物流を実現するために

- 現場
西村 良博
(ニシムラ ヨシヒロ)
阪神支店 次長(取材当時)
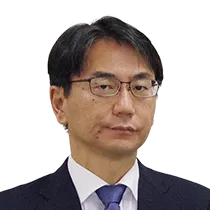
- 営業
津禰鹿 英樹
(ツネカ ヒデキ)
大阪営業第一部 次長(取材当時)
新規クライアント獲得の可能性を求めて
‐始まりは20年前、1本の電話から‐
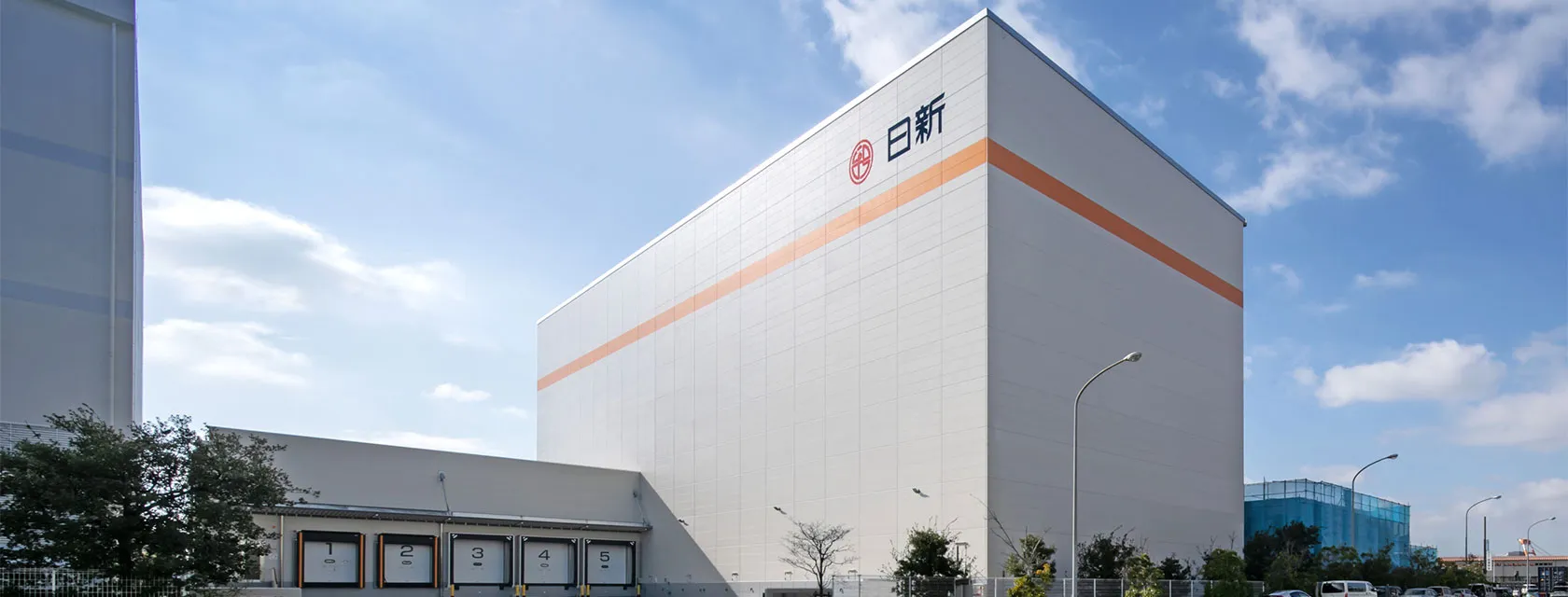
“安全”かつ“品質”が求められる食品物流。スーパーマーケットは私たちの暮らしに必要不可欠な社会インフラとして確立している。消費者が口にするものを輸送するだけに、品質管理の徹底は最大の責務だ。食品を取り扱う倉庫施設や立地といったハード面だけではなく、知識とノウハウといったソフト面のどちらも絶えず進化が求められている。
1999年9月、日新では食品管理に必要な四温度帯(冷凍・冷蔵・定温・常温)を一箇所で扱うことのできる最新の食品倉庫を神戸港湾エリアに新設。新規クライアントの獲得に向けて営業を開始した。当時の営業担当で、現在は大阪営業第一部で次長を務める津禰鹿は需要がありそうな企業へアポイントをとった。しかし、食品物流の場合、食品メーカーと物流企業が一体となり物流体制を構築しながら事業を展開していくことが多く、新規倉庫が途中参入する余地はほとんどなかった。
- 津禰鹿
-
「当時、食品の輸入会社をリストアップして一社ずつ電話をするのですが、どの会社からも『事業立ち上げからお世話になっている企業があるので新規は必要ない。』と断られ、非常に悔しかったのを覚えています。ですが裏を返すと、物流体制の構築時期に参加できれば、恒久的な取引ができるのではないか、という期待もありました。」
そこで、ターゲットを“新規事業を立ち上げたばかりの食品会社”に絞ってアプローチを続け、その中の1本の電話からようやく商談機会を得たのが、業務用食材を中心に製造・販売・小売業を展開する地元の食品会社であった。同社は2000年に食料品のSPA事業(※)と、フランチャイズによるスーパーマーケット事業の展開を始めたばかりで、本格的な事業拡大に向けて長期的に取引できるパートナーを探していた。
-
SPA事業:小売業が製造の分野まで踏み込み、自社オリジナル商品の開発を行い、販売するビジネスモデル
社内を動かす担当の熱意、将来性に賭けた心意気
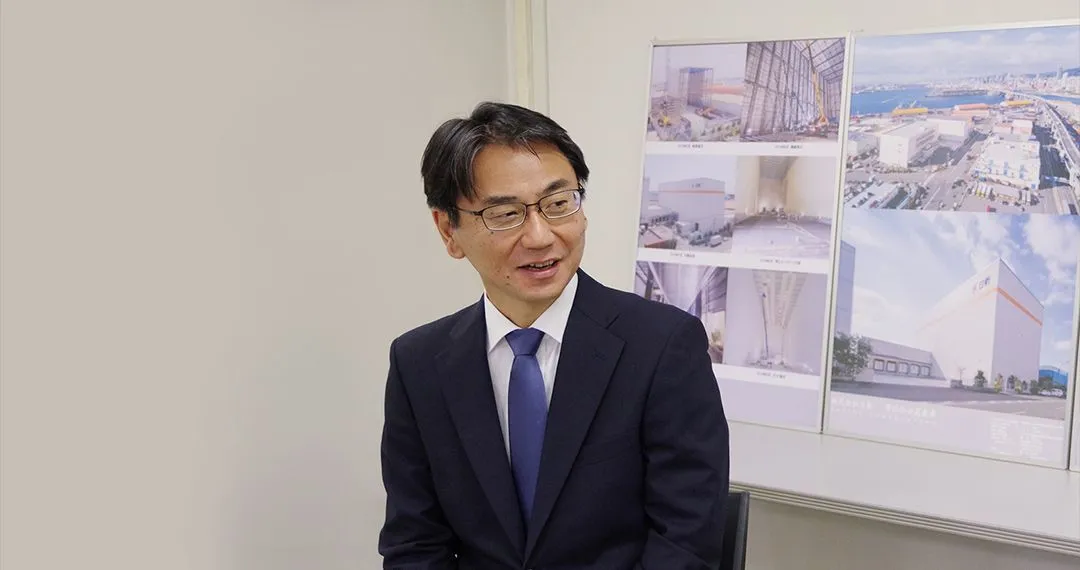
新設した倉庫の特徴とクライアントのニーズが合致し、大型契約のチャンスを得た日新だが、実はこの契約にあたり、これまで経験したことのない倉庫運営が求められることがわかった。従来はコンテナ輸送とコンテナから貨物を取り出すデバン作業を中心に展開する、いわゆる「川上の物流」のみ行ってきたが、店舗への納品、つまり川下まですべて自社で完結しなければならず、社内には慎重論が流れていた。
- 津禰鹿
-
「普段、港湾倉庫を運営する我々にとって、配送センターのように保管・仕分け・店舗別配送に至るまで全ての物流を担当する経験がこれまでなく、受注することに初めは否定的な意見が多かったです。ですが、クライアントと密に連絡していく中で、この事業の将来性に確信を持つようになり、社内の関係者の説得に回りました。すると、関係者全員が真剣に検討してくれ、『大変だが、やろう。』と言ってくれました。」
クライアント・営業・現場それぞれの思いが一つになり、2001年1月、作業内容や人材確保の面で目途が立ち、晴れて契約の運びとなった。
前代未聞の最難関オーダーに喰らいつく
圧倒的物量を支えた現場のプライド
初めてだらけの倉庫現場では、常に課題と向き合う挑戦の連続だった。
大躍進を続けるクライアントは、新店舗を続々と展開していく。貨物取扱量も右肩上がりに急増し、当時の使用可能スペースである7000t~8000tの貨物スペースは数年で限界に達しようとしていた。倉庫は満床にしないと利益を上げられないが、満床をキープしながら倉庫を回す。少しのアクシデントがあれば溢れてしまう状況だった。
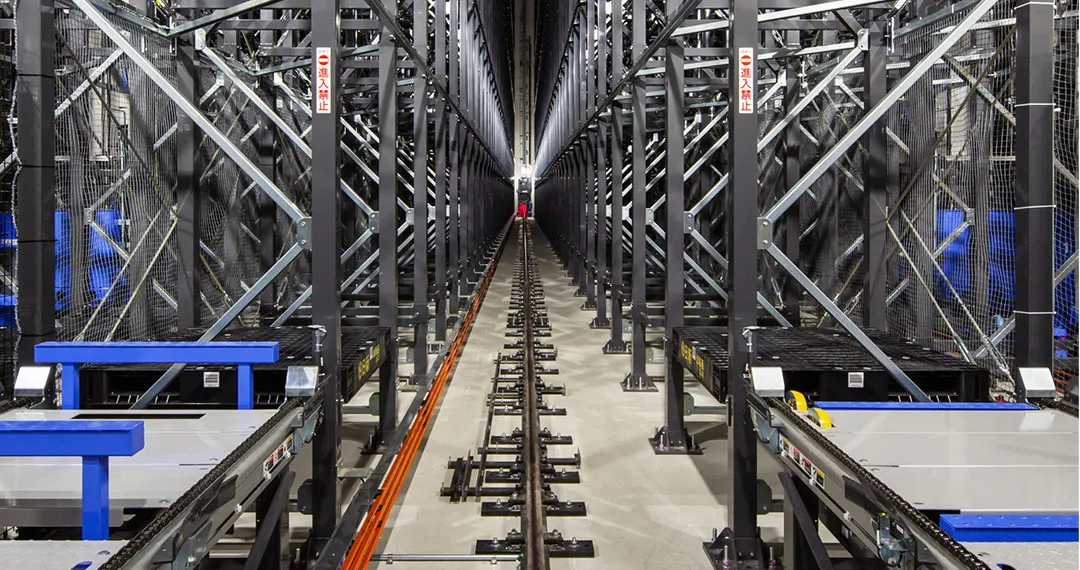
- 西村
-
「これまで経験したことのないほどの物量が来てしまい、余裕のない状況が続いていました。クライアントに『これ以上は無理です。』と断るのは簡単ですが、会社を背負っているというプライドがありましたので、絶対にギブアップしたくなかったのです。」
当時の現場担当で、現在は関西地区の倉庫部門で次長を務める西村は、すぐに周辺にある同業の倉庫会社に連絡を取った。日頃は同業他社より再保管寄託貨物を受けることもあるが、今回は委託側として貨物の再保管ができないか依頼した。検討の末、貨物の引き受けをお願いできるようになり、クライアントからのオーダーに対応することができた。
だが、もう一つの課題があった。
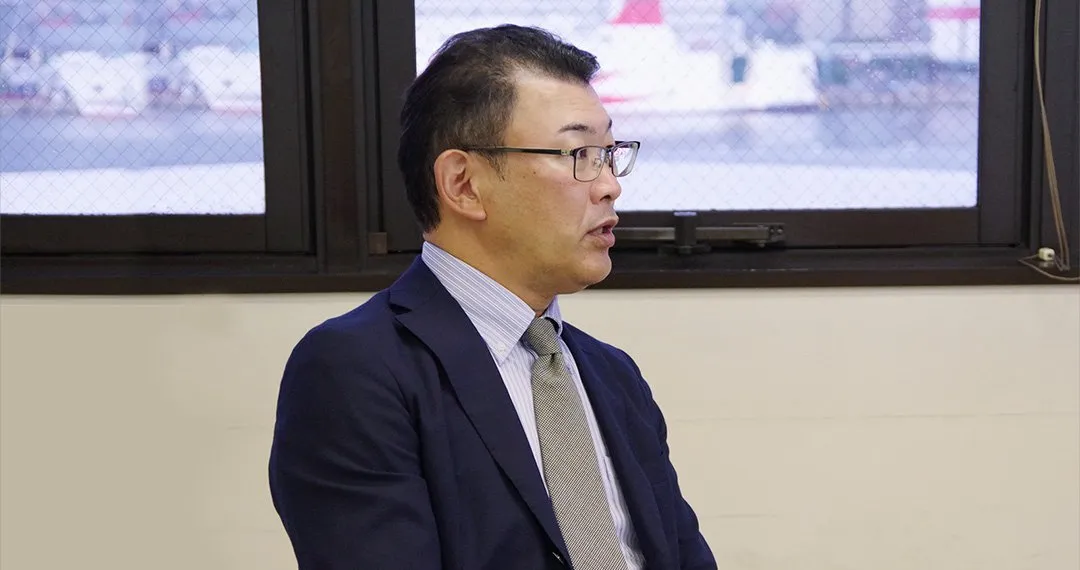
慣れない業務に加え、取扱い貨物が増えることで作業工程がさらに複雑になった。当初はスタッフがカゴ台車に載せて店別仕分、ピッキング作業を行い、似たような商品や新規の貨物が有れば都度クライアントへ確認する。出庫処理や入庫処理ではアナログでの作業を行っていくが、徐々に余裕がなくなってきた。そこで西村は社内でシステム開発を行う部門に協力を仰ぎ、倉庫管理システムをEDI化(※)することで効率化を図った。また、現場作業員や担当社員に対し、貨物知識の教育を行った。クライアントと同程度の知識を持った状態で、相手の立場に立ち、能動的に行動するように現場を指導した。それでも倉庫がいっぱいで貨物が今すぐに入らない場合は、営業と連携し事前にクライアントへ交渉、時間調整を行う等、流通が滞らないよう奔走した。
- 西村
-
「倉庫の切り盛りをするのが現場の仕事ですが、クライアントを納得させるのは営業の仕事。どちらが欠けてもうまくいきません。どんなに些細なことでも営業と相談し一体となって対応策を考え、クライアントに納得してもらえるよう努力しました。」
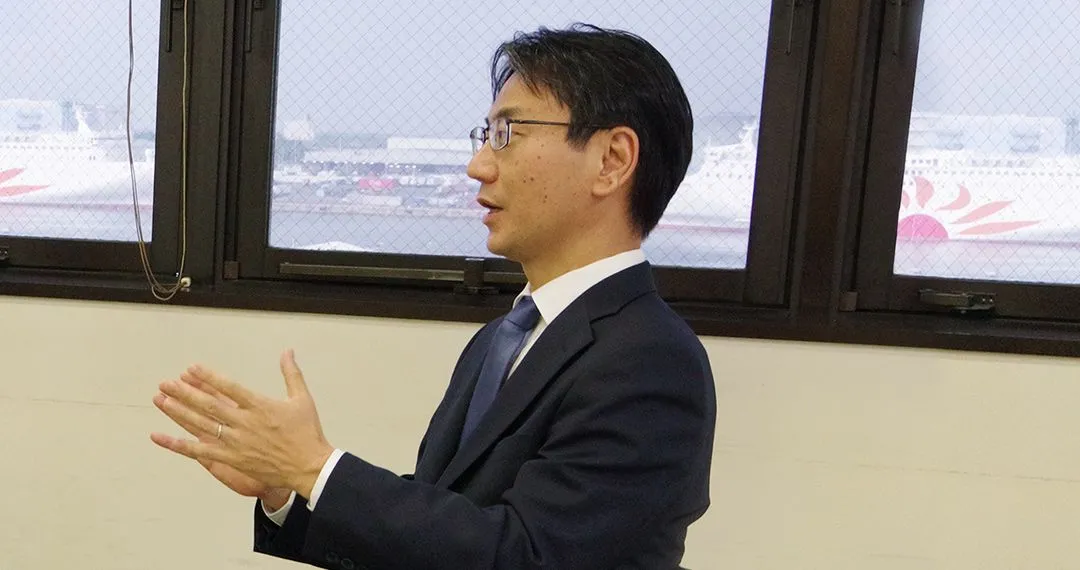
こうした課題を乗り越え、フランチャイズ事業がさらに急伸すると、2007年にはクライアント自らが隣接エリアに物流センターを新設。以降、保管業務と複数店舗毎のトータル出庫は日新、店別仕分・ピッキング業務はクライアントの担当という形で業務の棲み分けがなされ、今までの知識を最大限に活かすことのできる理想の物流体制を確立することができた。
- 西村
-
「大変な作業ばかりでしたが、これだけの物量を毎日捌ききったという達成感は大きかったですね。また社内だけでなく自家営業を行っていたことで社外の同業他社とも友好的な関係を築くことができました。この大型プロジェクトの山を乗り越えたことで、多少大きな物量がきても動じない冷静さが身に付き自信につながりました。クライアントの要求に最大限努力した結果が、品質の良さや、毎日店舗に商品が並んでいるといった“当たり前の日常”を支えているのだと思いますし、そのような経験ができるのが現場の魅力だと思っています。」
-
EDI化:電子データ交換(Electronic Data Interchange)の略で、お互いの各種取引データ(受発注・出荷・請求・支払いなど)を企業間で専用回線(オンライン含む)を通じてやり取りする仕組みのこと。
これまで共に歩んできた実績を基に将来を約束
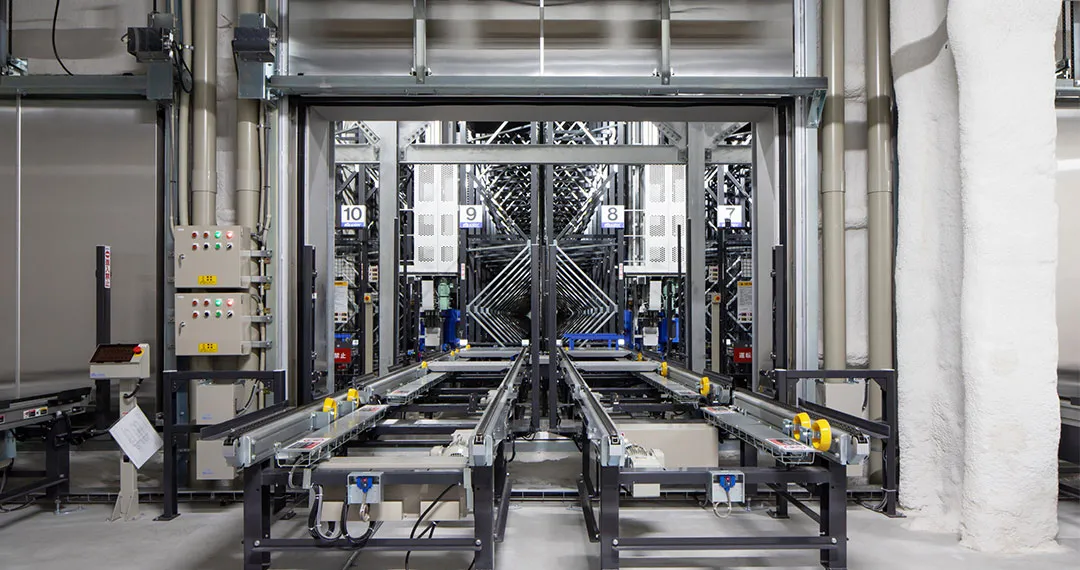
その後も低温カテゴリーを中心に順調に需要増加が続く中、クライアントと商談を重ねていくうち将来の事業計画に基づくさらなる倉庫需要の話が持ち上がった。そこで2018年3月、既存倉庫の隣にもう一棟、クライアント仕様の冷蔵倉庫の建設を決定。よりスピーディーな作業が可能になるように自動ラックを導入し、倉庫の格納場所の効率化、コンピュータ制御による正確かつ効率的な倉庫保管が可能となった。自動化により、-20℃以下という厳しい作業環境の改善や、少子高齢化による将来的な人手不足にも備えが利くようにもなる。またBCP対策(※)にも配慮しており、災害リスクにも対応している。
2020年2月に摩耶西冷蔵倉庫が竣工し、隣接する既存の摩耶冷蔵倉庫・摩耶埠頭倉庫と一体的に運用することで、四温度帯すべてに対応できる最先端の総合物流センターとして、多彩なサービスと充実したサポート体制が期待されている。
- 西村
-
「デリケートな対応が不可欠な食品では、四温度帯それぞれの特性を熟知していなければ最適な商品管理はできません。我々ひとりひとりが『現場のスペシャリスト』としてのプライドを持ち、安心して預けていただける倉庫になるように心がけています。今回のミッションは従来の倉庫事業とは全く異なるもので、次々と課題が浮上する中で、時代の変化や多様なニーズへの対応が必要でした。最初は苦労していた作業も、今ではIT、IoT化されてきています。とてつもない速さで変化する物流に対しても、変わらぬ積極的な姿勢で対応し進化を追求していくことが、我々の社会的役割だと考えています。」
-
BCP対策:企業が予測不可能な緊急事態(自然災害、事故、停電など)に見舞われた際に、重要業務の被害を最小限に抑え、企業運営を滞らせないための対策
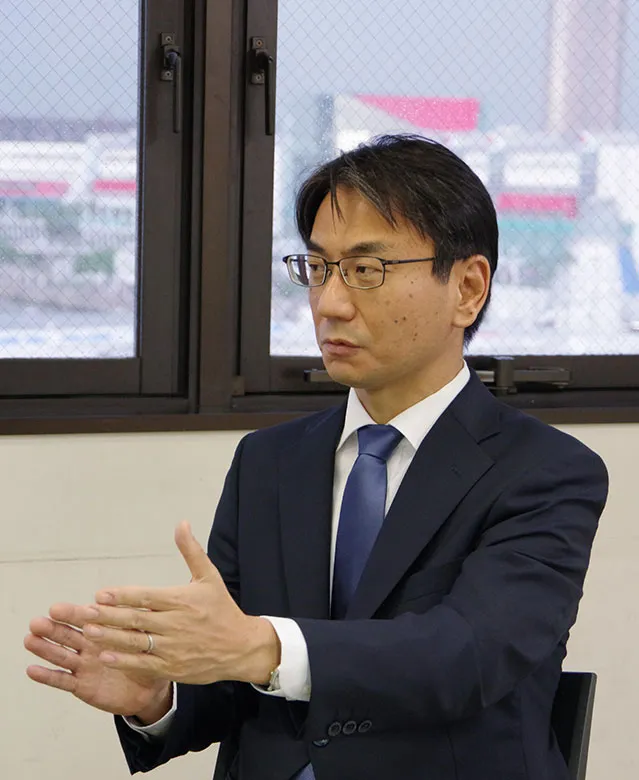
社内一丸となって物流の進化を実践
クライアントからの厚い信頼が誇り
冷蔵倉庫新設を契機に、ほぼゼロからスタートした新しい食品物流サービス。そのきっかけを作った営業部の津禰鹿は、これまでの20年を振り返り、進化の要因を次のように振り返る。
- 津禰鹿
-
「この食品物流サービスが20年間でここまで進化できたのは、営業と倉庫現場、そして、クライアントが同じ目標に向かって一丸となって試行錯誤を重ねてきた結果に尽きると思います。また、この間様々な課題に直面しましたが、そのたびに乗り越えることができたのは、物流体制構築の最初の段階からクライアントが求めるものに倉庫現場が真摯に向き合ってきたことで、良好なパートナーシップが構築されていたからに違いありません。今でもライバルと競い合っている状況に変わりはありませんが、クライアントから“お世話になっている会社”と呼んでいただけることが、いつも私達の励ましとなっています。」
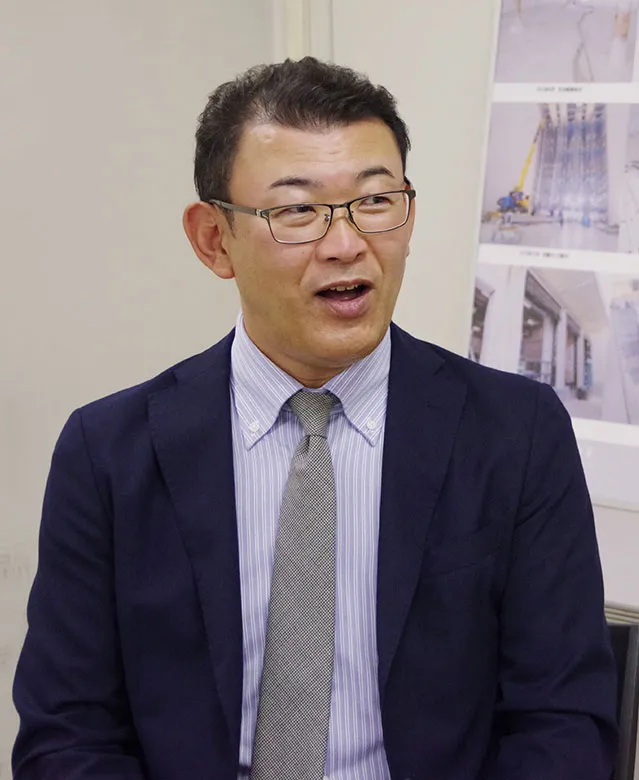
何があっても止められない食品物流
やりがいのある拠点は世界に
一方、倉庫現場でスタッフやシステム部門ときめ細かな調整を図ってきた西村は、まさに “現場のスペシャリスト”という存在だ。西村が日新を目指す学生たちに求めることは何か。
- 西村
-
「昨今の豪雨災害や世界的な感染症による社会の変化に限らず、どんな困難な状況があっても、食品物流は社会にとって不可欠なインフラです。営業から現場まで、世界中に働き甲斐のある拠点が色々ある。学生の皆さんには、自分の強みや特性を見つけ、グローバルな世界でやりたいことにぜひチャレンジしてほしいと思います。」
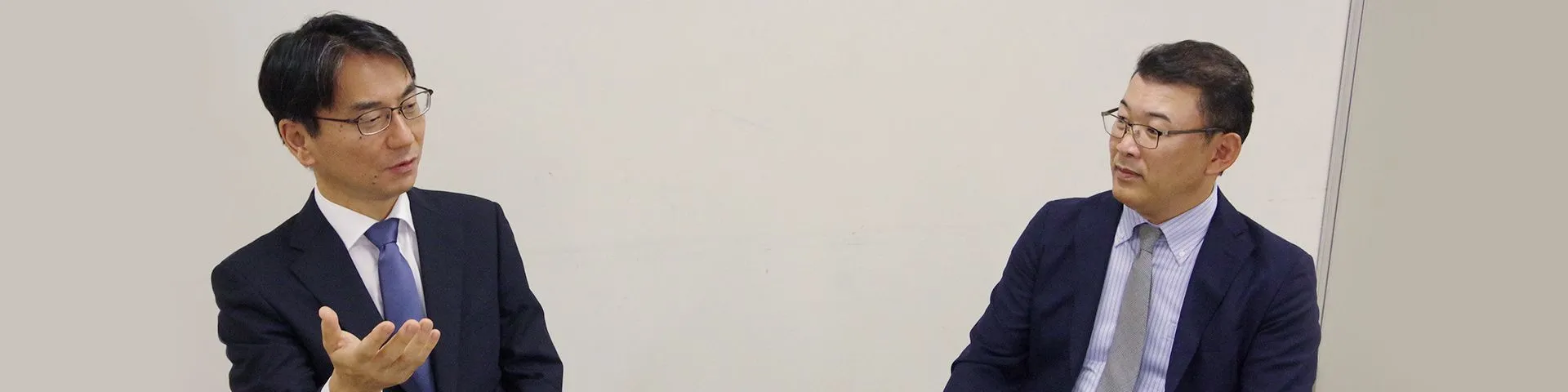
Another Story
まずはお気軽にお問い合わせください。担当営業より詳しくご説明させていただきます。